Spis treści
Co to jest precyzyjne cięcie metalu?
Precyzyjne cięcie metalu to nowoczesna metoda obróbcza, która gwarantuje niezwykłą dokładność oraz doskonałą jakość krawędzi. Do realizacji tego procesu wykorzystuje się różnorodne techniki, takie jak:
- cięcie laserowe,
- cięcie wodne,
- cięcie plazmowe.
Techniki te umożliwiają tworzenie skomplikowanych kształtów przy minimalnych stratach materiałowych. Gładkie krawędzie odgrywają kluczową rolę, wpływając zarówno na estetykę, jak i funkcjonalność gotowych elementów metalowych. Co więcej, precyzyjne cięcie zapewnia powtarzalność, co jest szczególnie ważne w produkcji seryjnej. Wysokiej jakości elementy, uzyskiwane dzięki temu procesowi, zmniejszają konieczność dodatkowej obróbki, co z kolei pozwala na redukcję kosztów produkcji oraz zwiększenie efektywności. W przemyśle ta metoda znajduje szerokie zastosowanie, na przykład w produkcji maszyn, elementów konstrukcyjnych i detali dekoracyjnych, gdzie wymagana jest wysoka tolerancja wymiarowa.
Dlaczego precyzja jest ważna w cięciu metalu?
Precyzyjne cięcie metalu odgrywa kluczową rolę w osiąganiu wysokiej jakości krawędzi. Jest to szczególnie istotne w sektorach, gdzie wymagana jest zarówno dokładność, jak i efektywność. Poprawne wypalanie elementów metalowych przyczynia się do zmniejszenia strat materiałowych, co z kolei obniża koszty produkcji. Każda nieścisłość może być źródłem problemów z dopasowaniem, co ma wpływ na całą konstrukcję.
Dodatkowo, precyzyjne cięcie ułatwia automatyzację, co zwiększa powtarzalność procesów i minimalizuje ludzkie błędy. Wykorzystanie różnych technologii cięcia, takich jak:
- lasery,
- cięcie wodą,
- plazmowe,
gwarantuje nie tylko wysoką jakość, ale również obfite możliwości projektowe. Dzięki precyzyjnemu podejściu, seryjnie produkowane elementy charakteryzują się odpowiednimi wymiarami, co jest niezwykle ważne w takich branżach, jak:
- lotnictwo,
- medycyna,
- motoryzacja.
gdzie tolerancje są niezmiernie rygorystyczne. Taka dokładność skutkuje również mniejszą ilością odpadów oraz ograniczonym zapotrzebowaniem na dodatkową obróbkę wykończeniową. Efektem końcowym jest zatem znacząca poprawa efektywności całego procesu produkcyjnego.
Jakie są rodzaje cięcia metalu?
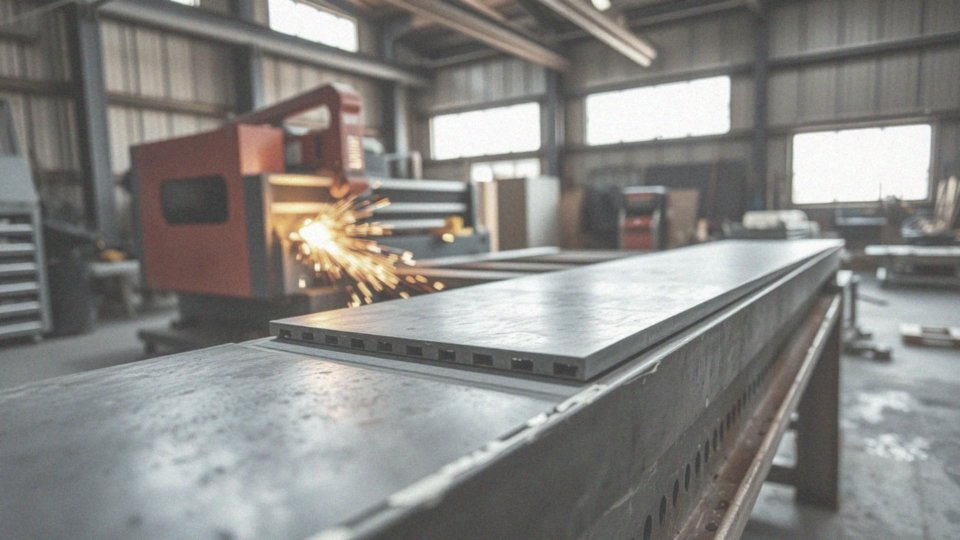
Cięcie metalu można klasyfikować na różne sposoby, w zależności od zastosowania oraz technik. Na początek warto zwrócić uwagę na cięcie termiczne, które obejmuje takie metody, jak:
- cięcie laserowe,
- cięcie plazmowe,
- cięcie tlenowe.
W przypadku cięcia laserowego wykorzystywana jest skoncentrowana energia świetlna, co pozwala na precyzyjne i gładkie cięcia, jednocześnie minimalizując odpady materiałowe. Z kolei cięcie plazmowe wykorzystuje gorący strumień gazu, który skutecznie topnieje metal, usuwając przy tym zbędny materiał. Inną grupą metod jest cięcie mechaniczne, w ramach którego stosuje się narzędzia takie jak:
- gilotyna,
- piły,
- nożyce.
Te techniki są doskonałe do prostych cięć i znajdują szerokie zastosowanie w branży budowlanej oraz obróbczej. Gilotyna, na przykład, umożliwia precyzyjne cięcie dużych arkuszy metalu. Kolejną nowoczesną metodą jest cięcie wodą, w tym cięcie hydroabrazywne. Ta technika opiera się na strumieniu wody pod ciśnieniem, co zapewnia wysoką precyzję i minimalizuje ryzyko deformacji materiału. Ostatnią z omawianych metod jest cięcie elektroerozyjne, które doskonale sprawdza się w obróbce trudnych metali, takich jak tytan. Dzięki tej metodzie możliwe jest dokładne cięcie małych detali, co czyni ją idealną dla zaawansowanych zastosowań przemysłowych. Dobór odpowiedniej metody cięcia uzależniony jest od specyficznych wymagań projektu, charakterystyki metalu oraz oczekiwań dotyczących jakości krawędzi.
Jakie są najpopularniejsze metody cięcia metalu?
W przemyśle metalowym istnieje wiele metod cięcia, które zostały opracowane z myślą o różnych potrzebach. Do najważniejszych metod należą:
- cięcie laserowe – wyróżnia się niezwykłą precyzją oraz wydajnością, idealne do tworzenia skomplikowanych kształtów oraz obróbki cienkowarstwowych materiałów. Dzięki skoncentrowanej wiązce światła można uzyskać gładkie krawędzie, co znacznie redukuje konieczność dalszej obróbki,
- cięcie plazmowe – doskonałe do grubych metali, umożliwia szybkie oraz skuteczne przecinanie elementów dzięki gorącemu strumieniowi plazmy. Znajduje zastosowanie w budownictwie i przemyśle ciężkim, gdzie czas oraz efektywność pracy są szczególnie istotne,
- cięcie wodą – nowoczesna opcja, która sprawdza się przy materiałach wrażliwych na wysoką temperaturę. Stosuje strumień wody pod dużym ciśnieniem, wzbogacony cząstkami ściernymi, co pozwala na precyzyjne cięcie bez ryzyka deformacji, gwarantując wysoką jakość krawędzi,
- cięcie tlenowe – chociaż nie jest tak powszechne, wciąż stanowi skuteczne rozwiązanie dla grubych stalowych elementów, w sytuacjach, gdzie inne metody mogą nie być wystarczająco efektywne,
- cięcie mechaniczne – wykorzystujące piły tarczowe czy szlifierki kątowe, prowadzi prostsze operacje. Mimo że nie jest tak dokładne jak cięcie laserowe czy wodne, znajduje zastosowanie w licznych branżach.
Wybór odpowiedniej metody cięcia metalowego zależy od specyfiki danego projektu, grubości wykorzystywanych materiałów oraz oczekiwań co do jakości krawędzi. Zrozumienie różnic pomiędzy tymi technikami ma kluczowe znaczenie dla efektywności pracy oraz uzyskiwanych rezultatów.
Na czym polega cięcie metalu laserem?
Cięcie metalu za pomocą lasera to nowoczesna technika, która wykorzystuje skoncentrowaną wiązkę laserową do nagrzewania i topnienia metalu w wybranym miejscu. W tym procesie kluczową rolę pełnią gazy techniczne, takie jak:
- azot,
- tlenu,
- które pomagają w usuwaniu stopionego materiału z linii cięcia,
- co skutkuje uzyskaniem idealnie gładkich krawędzi.
Dzięki temu jakość wyprodukowanych elementów znacząco wzrasta. Ta technologia wyróżnia się niezwykłą precyzją, co pozwala na realizację nawet najbardziej skomplikowanych wzorów, a jednocześnie ogranicza strefę wpływu ciepła. Laserowe maszyny tnące potrafią pracować na różnych rodzajach materiałów, w tym:
- blachach,
- profilach,
- oraz rurach.
Co istotne, ich duża powtarzalność jest kluczowym atutem w przemyśle maszynowym i budowlanym. Wysoka jakość cięcia laserowego nie tylko podnosi efektywność produkcji, ale również przyczynia się do zmniejszenia ilości odpadów. Elementy metalowe wycinane tą metodą wymagają zaledwie minimalnej dalszej obróbki, co w rezultacie prowadzi do realnych oszczędności w całym procesie produkcyjnym. Dlatego cięcie laserowe zyskuje status nie tylko sposobu na precyzyjne uzyskiwanie krawędzi, ale także jako efektywna metoda obróbcza, doceniana w wielu sektorach przemysłowych.
Jak działa cięcie metalu wodą?
Cięcie metalu za pomocą wody to nowoczesna metoda, w której wykorzystuje się strumień wody pod wysokim ciśnieniem do precyzyjnego przecinania metalu. Często do wody dodaje się ścierniwo, takie jak elektrokorund, co znacząco poprawia efektywność tego procesu. Strumień działa niczym narzędzie ścierne, dokładnie usuwając materiał.
Technika ta jest szczególnie efektywna w przypadku materiałów wrażliwych na wysoką temperaturę, gdyż zapobiega ich nagrzewaniu się. To istotne, zwłaszcza przy cięciu aluminium, ponieważ chroni przed odkształceniem i zapewnia doskonałą jakość krawędzi. Metoda cięcia wodą gwarantuje, że materiał pozostaje nietknięty, co ma kluczowe znaczenie w sytuacjach wymagających precyzji oraz wysokiej jakości.
Ponadto, pozwala ona na uzyskanie skomplikowanych kształtów i może być stosowana z różnorodnymi materiałami, co czyni ją niezwykle wszechstronną. Krawędzie uzyskiwane w tym procesie zazwyczaj nie wymagają dodatkowej obróbki, co z kolei podnosi efektywność produkcji. Dzięki swoim licznym zaletom, cięcie wodą zyskuje coraz większe uznanie w rozmaitych branżach przemysłowych.
Jakie są zalety cięcia metalu plazmowego?
Cięcie metalu plazmowego to niezwykle efektywna technika obróbcza, która oferuje mnóstwo korzyści. Kluczową cechą tej metody jest imponująca prędkość, wynikająca z użycia gorącego strumienia plazmy. Dzięki temu można z łatwością i precyzyjnie pracować z grubymi blachami, co jest niezwykle korzystne w sektorze przemysłu ciężkiego.
Warto dodać, że w porównaniu do cięcia laserowego, cięcie plazmowe wiąże się z niższymi kosztami eksploatacji, ponieważ nie wymaga drogich gazów szlachetnych, co znacząco obniża wydatki.
Kolejnym atutem tej metody jest jej uniwersalność; plazma świetnie radzi sobie z różnymi rodzajami metali, takimi jak:
- stal,
- aluminium,
- miedź.
Dlatego znajduje zastosowanie w wielu branżach, począwszy od budownictwa, a skończywszy na motoryzacji. W procesie cięcia plazmowego automatyzacja odgrywa istotną rolę, zwiększając efektywność i minimalizując ryzyko popełnienia błędów. Dzięki temu realizacja zleceń produkcyjnych staje się szybsza i bardziej płynna.
Obsługa urządzeń plazmowych jest na tyle prosta, że technika ta staje się coraz bardziej dostępna dla licznych zakładów produkcyjnych, co ułatwia jej integrację z istniejącymi procesami. Umożliwia to prowadzenie ciągłej produkcji, co z kolei zwiększa wydajność i umożliwia realizację większych zamówień bez długich przestojów.
W skrócie, cięcie plazmowe łączy w sobie szybkość, efektywność, wszechstronność oraz opłacalność, co czyni je nieodzownym narzędziem w nowoczesnej obróbce metalu.
Jakie są różnice między cięciem tlenowym a cięciem plazmowym?
Cięcie tlenowe i plazmowe to dwie różne metody obróbcze, które mają swoje unikalne cechy i zastosowania. Proces cięcia tlenowego oparty jest na spalaniu metalu przy użyciu czystego tlenu, który jest szczególnie skuteczny w obróbce stali niskowęglowych. Choć wymaga wcześniejszego podgrzania materiału, co może wydłużać czas pracy, to wciąż pozostaje jedną z bardziej ekonomicznych opcji. Zastosowanie palnika gazowego oraz odpowiednich gazów technicznych pozwala na efektywne cięcie grubych stalowych elementów.
Z drugiej strony, cięcie plazmowe polega na wykorzystaniu łuku plazmowego do stopienia metalu. Ta technika jest bardziej uniwersalna, umożliwiając obróbkę różnorodnych materiałów, takich jak:
- stal nierdzewna,
- aluminium.
Charakteryzuje się znacznie szybszym procesem oraz lepszą jakością cięcia. Mniejszy wpływ ciepła na materiał sprzyja precyzyjniejszym efektom końcowym w porównaniu do cięcia tlenowego. Choć cięcie plazmowe cieszy się dużym uznaniem, zwłaszcza w przemyśle ciężkim, cięcie tlenowe nadal ma swoje miejsce, szczególnie tam, gdzie kluczowym czynnikiem są koszty – jak w przypadku obróbki masywnych elementów.
Wybór odpowiedniej metody cięcia powinien zatem uwzględniać specyfikę projektu oraz różnice w jakości, wydajności i kosztach obróbczych.
Jakie narzędzia można wykorzystać do cięcia metalu?
Narzędzia do cięcia metalu są niezwykle zróżnicowane, różnią się zarówno zastosowaniem, jak i precyzją oraz grubością ciętego materiału. Oto kilka z najczęściej używanych:
- Szlifierki kątowe – uniwersalne urządzenia, które cieszą się dużą popularnością w obrębie obróbki metalu, znakomicie sprawdzają się w cięciu blach oraz profili metalowych,
- Piły tarczowe – doskonale nadają się do wykonywania prostych cięć w metalowych materiałach, użycie tarcz z żywic syntetycznych znacząco podnosi ich efektywność,
- Wyrzynarki – pozwalają na precyzyjne cięcie przy zastosowaniu specjalistycznych brzeszczotów przeznaczonych do metalu, są niezastąpione w sytuacjach, gdy wymagana jest wysoka dokładność,
- Nożyce do blachy – idealne do cięcia blach stalowych i aluminiowych, działają zarówno w wersji manualnej, jak i elektrycznej, co czyni je bardzo wszechstronnymi,
- Gilotyny – rewelacyjnie sprawdzają się przy cięciu dużych arkuszy metalu, zwłaszcza w produkcji seryjnej, gdzie wydajność jest kluczowa,
- Palniki gazowe – wykorzystywane do cięcia tlenowego, najczęściej wybierane do grubych elementów stalowych,
- Maszyny do cięcia laserowego – oferują wyjątkową precyzję oraz doskonałą jakość krawędzi, są idealne do skomplikowanych kształtów i cienkowarstwowych materiałów,
- Maszyny do cięcia plazmowego – umożliwiają szybkie cięcie grubych metali, co przynosi korzyści w branży ciężkiej.
Wybór odpowiednich narzędzi powinien być dostosowany do rodzaju metalu oraz specyfiki konkretnego projektu. Odpowiednia selekcja narzędzi nie tylko zwiększa efektywność, ale także jakość całego procesu produkcji.
Dlaczego cięcie metalu wymaga odpowiednich narzędzi i technik?
Cięcie metalu to proces, który wymaga zastosowania właściwych narzędzi oraz technik, by zapewnić zarówno bezpieczeństwo, jak i wysoką jakość krawędzi. Niewłaściwy wybór narzędzi może prowadzić do:
- poważnych uszkodzeń materiału,
- pojawienia się zadziorów,
- odkształceń,
- negatywnego wpływu na dalszą obróbkę.
Na przykład, podczas cięcia stali nierdzewnej istotne jest, by korzystać ze specjalistycznych ostrzy, które zapobiegają przegrzaniu materiału, ponieważ to może osłabić jego strukturę. Nowoczesne metody cięcia, takie jak:
- cięcie laserowe,
- cięcie wodne,
pozwalają uzyskać gładkie krawędzie oraz złożone kształty przy minimalnych stratach surowca. Dzięki tym technologiom zwiększa się efektywność produkcji, a jednocześnie redukuje odpady. Narzędzia stosowane do cięcia, takie jak:
- gilotyny,
- szlifierki kątowe,
- maszyny do cięcia plazmowego,
mają kluczowe znaczenie dla precyzji wycinanych elementów. Przy wyborze odpowiedniej metody cięcia istotne jest uwzględnienie właściwości materiału oraz wymagań związanych z jakością krawędzi. Takie podejście nie tylko poprawia bezpieczeństwo w miejscu pracy, ale także wpływa na koszty produkcji. Odpowiednio dobrane techniki cięcia pomagają zaoszczędzić, ponieważ zmniejszają potrzebę dalszej obróbki. Dlatego różnorodne metody cięcia mają fundamentalne znaczenie w wielu branżach, w których precyzja i jakość są kluczowe.
Jakie czynniki wpływają na jakość krawędzi cięcia?
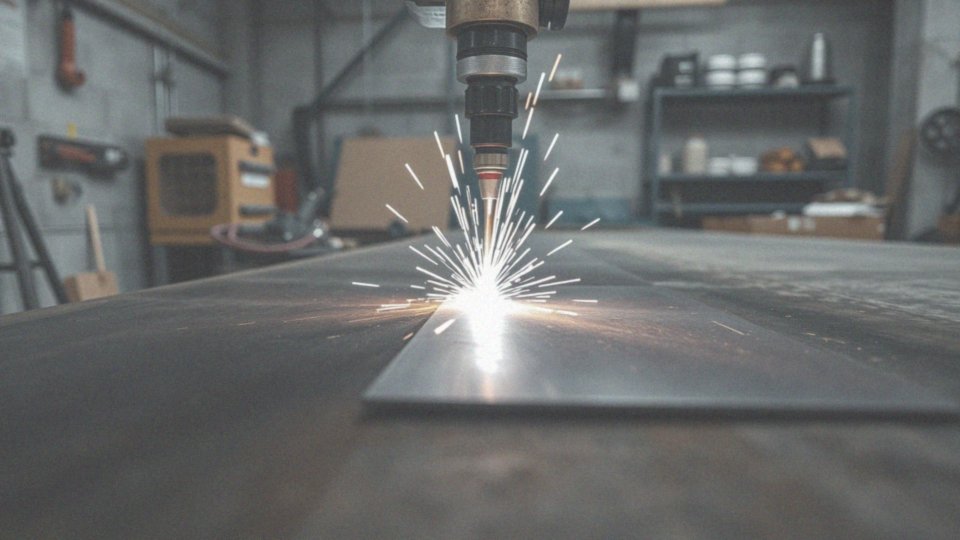
Jakość krawędzi cięcia jest determinowana przez szereg czynników, które warto dokładnie przeanalizować podczas obróbki metalu. Kluczowym elementem jest wybór odpowiedniej metody cięcia, na przykład:
- cięcie laserowe,
- cięcie wodne,
- cięcie plazmowe.
Każda z tych technik dysponuje różnymi parametrami, które wpływają na końcowy efekt. Moc lasera, ciśnienie wody oraz natężenie prądu plazmowego to istotne wartości, które należy starannie ustawić. Zmiany w tych parametrach mogą skutkować niezadowalającymi efektami.
Warto również pamiętać, że jakość narzędzi tnących, takich jak tarcze i dysze, ma ogromne znaczenie dla precyzji każdej krawędzi. Wysokiej klasy narzędzia przyczyniają się do zwiększenia dokładności cięcia oraz ograniczenia powstawania zadziorów. Również właściwości ciętego materiału, takie jak:
- twardość,
- skład chemiczny,
- rodzaj materiału.
mają wpływ na ostateczną jakość krawędzi. Na przykład podczas cięcia aluminium lub miedzi należy korzystać z odpowiednich narzędzi, aby uniknąć problemów z jakością wykonania. Ważna jest także stabilność oraz czystość procesu cięcia, co przekłada się na lepsze rezultaty.
Utrzymanie odpowiednich warunków roboczych, w tym efektywne chłodzenie, redukuje ryzyko uszkodzenia materiału i przekłada się na poprawę jakości. Na koniec, nie można zapominać o umiejętnościach operatora – doświadczeni profesjonaliści potrafią dostosować parametry cięcia do specyficznych warunków, co skutkuje satysfakcjonującą jakością krawędzi oraz wyższą jakością finalnych elementów.
Jakie zastosowania ma cięcie metalu w przemyśle?
Cięcie metalu odgrywa kluczową rolę w wielu dziedzinach, począwszy od budownictwa, aż po przemysł motoryzacyjny. W sektorze budowlanym ta technika umożliwia dokładne dopasowanie elementów konstrukcyjnych, co ma ogromne znaczenie w przypadku skomplikowanych struktur. W motoryzacji cięcie metalu jest niezbędne dla wytwarzania karoserii oraz różnych podzespołów, co z kolei wpływa na bezpieczeństwo oraz efektywność pojazdów.
W lotnictwie metody cięcia są stosowane do formowania komponentów samolotów, które muszą spełniać ścisłe normy dotyczące wagi i wytrzymałości. W przemyśle maszynowym precyzyjne cięcie jest kluczowe dla produkcji szczegółowych części, które z kolei przekładają się na jakość finalnych wyrobów. Nie można także pominąć znaczenia technik cięcia w produkcji mebli metalowych, gdzie odpowiedni wybór metod obróbczych wpływa na estetykę oraz funkcjonalność.
W branży reklamowej cięcie metalu pozwala na tworzenie atrakcyjnych liter oraz innowacyjnych elementów dekoracyjnych, które przyciągają wzrok potencjalnych klientów. Dzięki automatyzacji procesów cięcia zwiększa się wydajność oraz ogranicza ryzyko ludzkich błędów. Właściwy dobór takich technik jak cięcie laserowe, wodne czy plazmowe gwarantuje doskonałą jakość krawędzi, co jest niezwykle istotne w wielu branżach. Dlatego cięcie metalu stało się fundamentem obróbki blach, profili i rur, umożliwiając precyzyjne kształtowanie różnorodnych elementów metalowych.
Jakie są wady i zalety cięcia metalu szlifierką kątową?
Cięcie metalu za pomocą szlifierki kątowej ma swoje zalety i wady, które należy wziąć pod uwagę przy wyborze odpowiedniej metody obróbki. Jednym z głównych atutów tego narzędzia jest łatwość w obsłudze. Dzięki swojej mobilności, szlifierka może być stosowana w różnych lokalizacjach, co jest szczególnie ważne tam, gdzie dostęp do energii elektrycznej jest ograniczony. Ceny szlifierek kątowych są również przystępne, co czyni je popularnym wyborem wśród warsztatów, jak i hobbystów.
Z drugiej strony, cięcie szlifierką niesie ze sobą pewne ograniczenia:
- często brakuje jej precyzji, co może negatywnie wpłynąć na jakość krawędzi oraz ogólny wygląd obrabianego przedmiotu,
- proces ten generuje znaczną ilość hałasu oraz pyłu, co z kolei wiąże się z koniecznością stosowania odpowiednich środków ochrony osobistej,
- istnieje ryzyko przegrzania materiału, co prowadzi do jego deformacji, zwłaszcza przy grubszych elementach.
W sytuacjach, gdzie wymagana jest wysoka dokładność, na przykład przy wytwarzaniu detali maszynowych, bardziej sprawdzą się zaawansowane technologie, takie jak cięcie laserowe czy plazmowe. Dlatego przy wyborze metody cięcia warto uwzględnić charakterystyczne cechy projektu oraz oczekiwania dotyczące jakości i efektywności. Szlifierka kątowa doskonale sprawdza się w prostszych aplikacjach, ale w bardziej skomplikowanych przypadkach warto pomyśleć o innych technologiach.
Co sprawia, że cięcie wodą jest metodą nowoczesną?
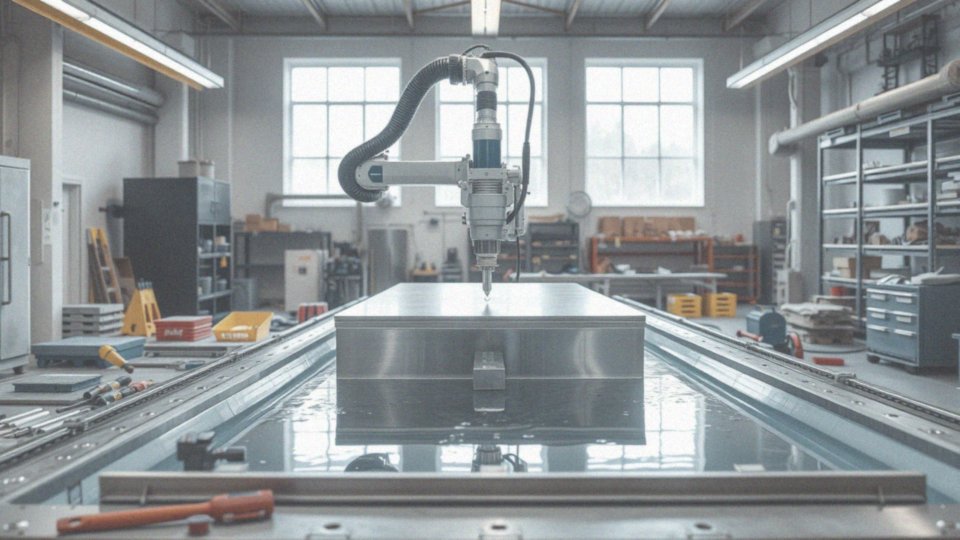
Cięcie wodą to nowoczesna technika, która zdobywa coraz większą popularność w branży przemysłowej. Co sprawia, że jest tak doceniana?
- zapewnia wyjątkową precyzję,
- działa bez wpływu ciepła na materiał,
- całkowicie eliminuje ryzyko deformacji,
- minimalizuje straty materiałowe, generując mniej odpadów,
- jest przyjazna dla środowiska, gdyż nie emituje szkodliwych gazów.
Proces ten przebiega na zimno, co jest istotne, szczególnie w przypadku obróbki aluminium oraz delikatnych kompozytów. Dzięki zastosowaniu strumienia wody pod wysokim ciśnieniem możliwe jest cięcie różnych materiałów – od metali, przez tworzywa sztuczne, aż do kamienia. Ta wszechstronność czyni cięcie wodą niezwykle praktycznym rozwiązaniem.
Wysoka jakość krawędzi wycinanych materiałów oznacza, że często nie jest konieczna dodatkowa obróbka, co prowadzi do znacznych oszczędności zarówno czasu, jak i kosztów. Dodatkowo, możliwość dostosowania ciśnienia oraz zastosowanie abrazyn pozytywnie wpływa na wydajność procesu. Cięcie wodą wyróżnia się nie tylko innowacyjnością, ale również zaawansowaniem technologicznym, co sprawia, że jest jedną z najbardziej efektywnych metod dostępnych obecnie na rynku.
Jakie materiały można ciąć przy pomocy cięcia laserowego?
Cięcie laserowe to innowacyjna metoda obróbcza, która umożliwia niezwykle precyzyjne dzielenie różnorodnych materiałów. Technologia ta sprawdza się doskonale w obróbce:
- stali węglowych,
- stali nierdzewnych,
- aluminium,
- miedzi,
- mosiądz,
- tytanu,
- tworzyw sztucznych.
Jej działanie opiera się na wykorzystaniu skoncentrowanej wiązki laserowej, co skutkuje uzyskaniem gładkich krawędzi – istotnych w licznych sektorach przemysłowych. Kluczowe jest odpowiednie ustawienie parametrów, takich jak moc lasera oraz rodzaje gazów technicznych. Na przykład, cięcie aluminium wymaga innych ustawień niż cięcie stali nierdzewnej, co ma na celu osiągnięcie jak najlepszej jakości krawędzi. Skuteczne zarządzanie tymi parametrami pozwala także na zmniejszenie ilości odpadów materiałowych oraz ogranicza konieczność dalszej obróbki.
Co więcej, cięcie laserowe znajduje zastosowanie w obróbce materiałów kompozytowych, co czyni tę technikę wszechstronnym rozwiązaniem w skomplikowanych aplikacjach. Dzięki tym zaletom zyskało ono spore uznanie w branżach:
- maszynowej,
- motoryzacyjnej,
- budowlanej.
Nieustannie obserwujemy rozwój wyspecjalizowanych procesów produkcyjnych, gdzie precyzja i jakość krawędzi mają kluczowe znaczenie.